5 Things To Consider When Deciding The Frequency Of Quality Control Inspections
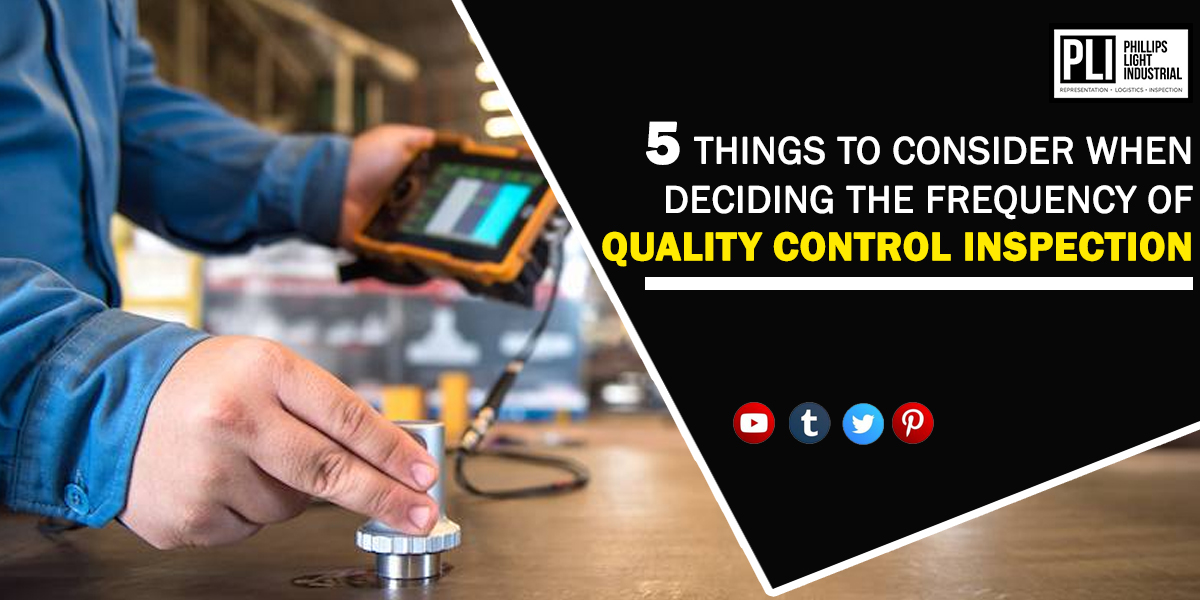
Quality control inspections play a pivotal role in ensuring the integrity and reliability of products and services across various industries. Whether you’re in manufacturing, construction, or any other sector, maintaining consistent quality standards is imperative. In Ohio, where industrial enterprises thrive, quality control inspection services are in high demand. To stay ahead of the competition, it’s crucial to consider the frequency of these inspections carefully. In this article, we, at PLI Sorting, explore the five key aspects to contemplate when determining the frequency of quality control inspection services in Ohio.
1. Industry Regulations and Standards
Quality control inspection services in Ohio must adhere to strict industry regulations and standards. The first factor to consider is the specific requirements of your industry. Regulations can vary significantly from one sector to another. For instance, aerospace and healthcare industries may require more frequent inspections due to the critical nature of their products. Understanding the compliance obligations within your field is paramount.
2. Product Complexity
The complexity of the products or services you offer can significantly influence the frequency of quality control inspections. Highly intricate products often necessitate more frequent evaluations. This is because the more complex a product, the higher the likelihood of defects or issues arising during the manufacturing or service delivery process. Industrial inspection companies in Ohio should assess the intricacy of their offerings to determine the appropriate inspection schedule.
3. Historical Data and Performance Metrics
Analyzing historical data and performance metrics is a valuable practice for optimizing the frequency of quality control inspections. By evaluating past records, you can identify patterns of defects or quality issues that may have emerged. These insights can help you pinpoint periods when inspections should be intensified or scaled back. A data-driven approach enhances efficiency and ensures that inspections are conducted when they are most needed.
4. Customer Feedback and Complaints
Your customers are an invaluable source of information when it comes to determining the frequency of quality control inspections. Pay close attention to customer feedback and complaints. Frequent complaints or returns may indicate a need for more rigorous inspections. Conversely, if customers consistently express satisfaction, it may be an opportunity to optimize your inspection schedule for efficiency.
5. Risk Assessment
A comprehensive risk assessment is fundamental to making informed decisions about quality control inspections. Identify potential risks associated with your products or services and assess their potential impact. High-risk items may require more frequent inspections to mitigate liabilities and ensure customer safety. Conversely, low-risk offerings can undergo less frequent evaluations, reducing operational costs.
In conclusion, the frequency of quality control inspections is a critical factor that can impact the success and reputation of your business. By carefully considering industry regulations, product complexity, historical data, customer feedback, and risk assessment, you can develop an effective inspection schedule that aligns with the specific needs of your enterprise. At PLI Sorting, we understand the importance of tailored quality control solutions for businesses in Ohio. Our dedicated team is committed to providing Ohio’s top-notch quality control inspection services.
For more information, please get in touch with us at +1(216) 440-6060 or email us at sales@phillipslightindustrial.com, and we will be there for you.
Recommended Posts
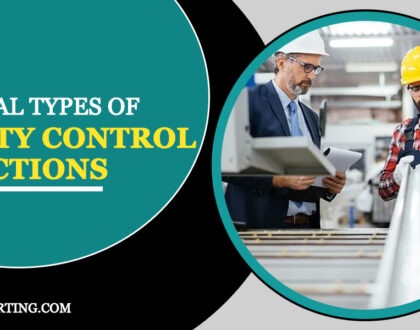
5 Critical Types of Quality Control Inspections
July 25, 2023